Case studies on this page…
- Chemical storage
- Multi-level car park
- Chiller equipment
- Boutique distillery
- Chemical and petroleum terminal facility
- Fertiliser storage
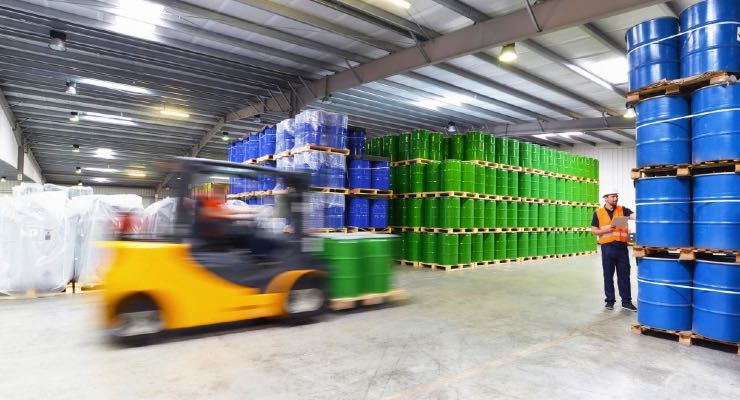
1. Chemical storage
The site
The site is a storage and distribution facility that handles a variety of chemicals for multiple industrial clients. Of the different chemicals on site the greatest risk of leak lies with ammonia and methyl bromide.
The challenge
In order to protect its own workforce and its neighbours, the site needs a fixed gas detection system that provides instant warning of any vapours being emitted.
Furthermore, the system needs a tailored response based on the concentration of gas detected; from a local alarm for a low-level detection, through to an automated call-out to Fire Emergency NZ to enact the emergency response plan, if required.
The solution
Entec worked collaboratively with this client to understand the complex requirements and to custom design a suite of fixed gas detection equipment. This includes a Teledyne Meridian fixed gas detector for ammonia, and multiple Uniphos fixed gas detectors for methyl bromide.
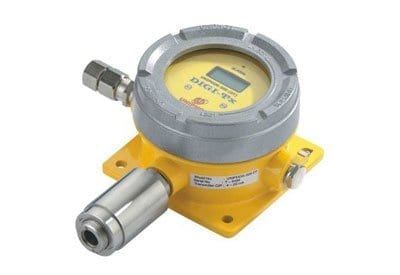
All detectors are connected to a common Teledyne Oldham MX43 controller, which activates local sounders and is also integrated into the site’s fire alarm panel.
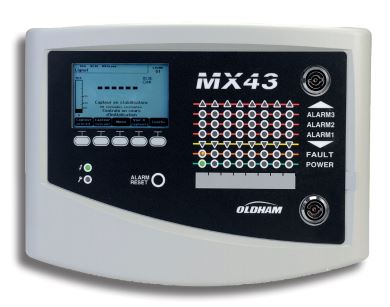
Ongoing success
Entec provides monthly on-site service to this client, during which we carry out bump testing of each detector and analyse the trends captured by the MX43 controller. This has enabled the system to be fine-tuned, and has provided useful data to the client to allow them to better understand any vulnerabilities in their process.
Entec also provides annual calibrations of all equipment as part of its service package. This calibration work is facilitated by the use of “plug and play” smart calibrated sensors.
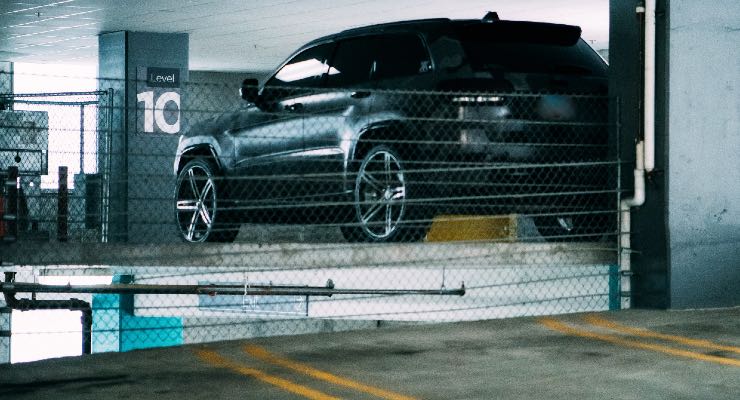
2. Multi-level car park
The site
The site is a large, multi-storey underground car park, used daily by commercial lessees and casual visitors.
The challenge
As with any confined car park, this facility had a carbon monoxide (CO) fixed gas detection system installed at the time of construction. Due to the size of the car park, the system comprised a ducted network operating under vacuum with 90 sampling points. The ducts return to a central location where two CO sensors were installed.
Each of the 90 points were intermittently passed across the CO sensors. A CO detection activates a ventilation fan in the sampled area to mitigate the CO build-up.
The system had been subjected to six monthly service by a building services contractor who didn’t fully understand the system design.
They had correctly been checking the operation of the CO sensors. However, they didn’t understand that due to an installation error, the CO sensors were never actually exposed to the sampled air.
Therefore, the system was not capable of actually detecting CO within the car park.
The solution
Entec was called to site to carry out routine service on the CO sensors. Upon investigation, the installation error was identified and corrected. The system has been reconfigured so that air from the 90 sampling points does indeed now pass across the CO sensors.
The issue was only detected because Entec’s service technician is a trained and experienced instrumentation technician. His enquiring mind saw something that didn’t quite look right, and he had the skills to investigate further.
Ongoing success
The CO fixed gas detection system is now operating correctly. Entec carries out six-monthly service visits during which the CO sensors are calibrated, and the whole system is checked to make sure that it is working as designed.
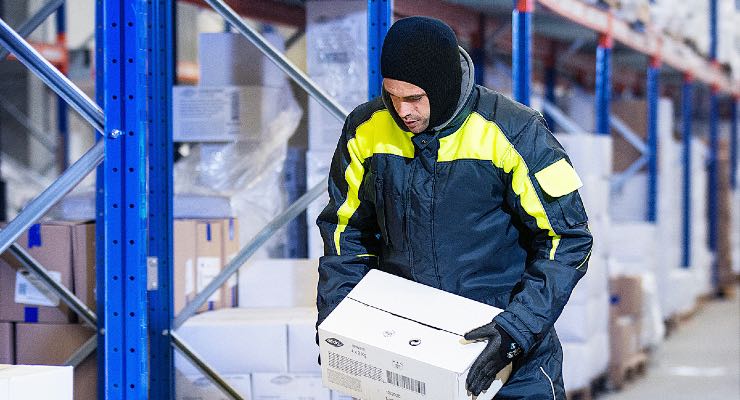
3. Chiller equipment
The site
The site is a storage and distribution facility for food and beverage products. The site includes a large chilled goods area.
The challenge
When Entec attended the site to carry out a routine service on the existing fixed gas detection system, the technician identified that a CO2 detector was incorrectly installed.
As CO2 is heavier than air, CO2 detectors must be installed proximate to the ground. The CO2 detector in this chiller room was near the ceiling and was never going to provide proper protection against a CO2 leak.
The solution
Once identified, it was a relatively simple exercise to relocate the CO2 detector to a more appropriate location, recommission the system and return it to service.
Ongoing success
Entec continues to provide routine service of the fixed gas detection at this site. Entec’s technicians do not simply perform detector calibrations and be on their way – they are interested in making sure the overall gas detection system will operate as designed.
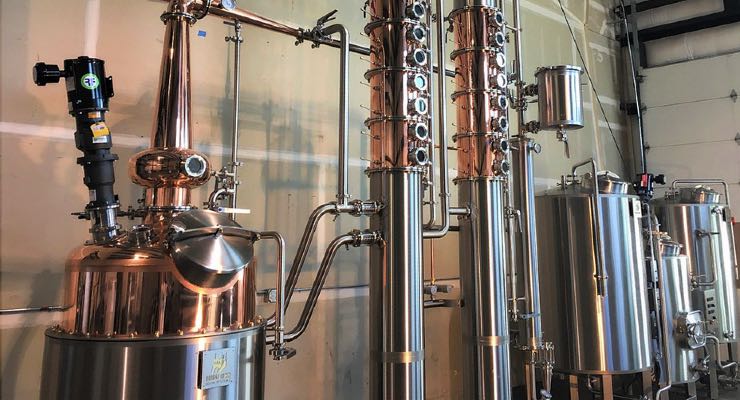
4. Boutique distillery
The site
The site is a newly built distillery producing high quality spirits. All parts of the production process are on site, from distilling to ageing, blending, bottling and warehousing.
The challenge
Ethanol is a natural by-product of the distilling process. Ethanol is a flammable liquid which can give off a vapour. Ethanol vapour, together with oxygen and a source of ignition, is highly explosive.
Ethanol is a class 3.1 (flammable liquid) hazardous substance. A HSNO regulation specifies building types and separation distances for the various flammable substances and the various quantities stored.
Electrical equipment must have the correct certification to be installed in these zoned areas.
The solution
Entec’s gas detection sales team was contacted at the time of construction. Entec supplied three Teledyne Oldham OLCT100 fixed gas detectors and an Oldham MX32 controller.
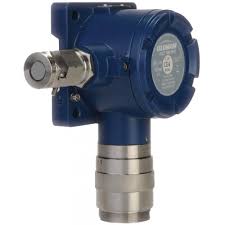
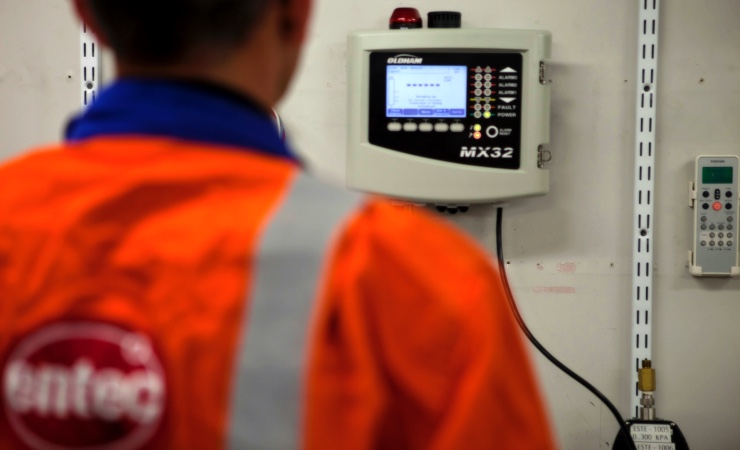
The detectors are LEL (configured for ethanol) – designed to detect ethanol in its gaseous form within the lower explosive level.
One of Entec’s primary activities is instrumentation and electrical installation work, specialising in hazardous area environments. Entec’s I&E team were therefore able to install and commission the fixed gas detection system.
The system provides local alarms in the event of an LEL detection and initiates an emergency shutdown of the process, isolating all sources of electricity.
Ongoing success
The fixed gas detection system is working as designed. The client carries out its own monthly bump testing to be assured of ongoing functionality, and Entec provides annual calibrations of the LEL sensors.
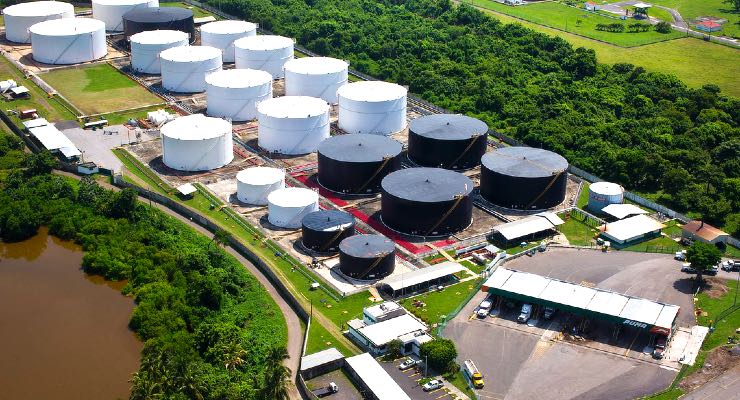
5. Chemical and petroleum terminal facility
The site
The site is a terminal facility that handles a variety of liquid products including methanol, ethanol, LPG and condensate.
The challenge
Due to its coastal location, the site is very exposed to weather and salt-laden air, making this an arduous environment for any equipment.
With multiple products being handled, and a variety of terminal activities taking place simultaneously, the site has many hazards to be mitigated. Installation and service activities need to be highly flexible to fit in around terminal operations.
The site had a legacy fixed gas detection system comprising many gas detector transmitters that were able to remain in service, and an older control system that required replacement.
The project was an interesting blend of integrating new equipment into some older infrastructure.
The solution
Over many years, Entec has supplied, installed and continues to service the fixed gas detection equipment at this terminal. There is a variety of equipment installed for the varied applications, with the majority of newer instruments being Teledyne Oldham Simtronic infrared LEL detectors.
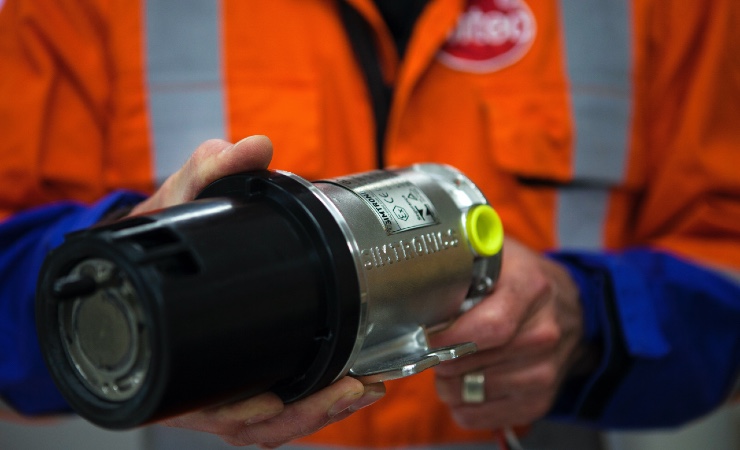
The system is now controlled by an Oldham MX32 controller. All equipment is hazardous area rated.
Ongoing success
The system is working as designed. With a strong working relationship in place between Entec and the client, our service technicians are able to adapt around the operational requirements of the site and help the client concentrate on its primary task – the storage and distribution of product with zero spills and zero harm.
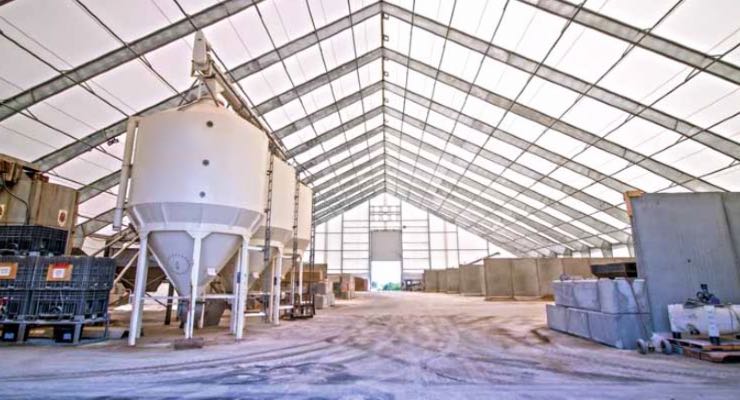
6. Fertiliser storage
The site
The site is a bulk store for fertiliser products. Individual ingredients are also stored on-site, and there is a limited amount of batch mixing to make final products.
The challenge
Entec attended this site for a service call on an existing fixed gas detection system. The system included a Sulphur Dioxide sensor. Unfortunately, this detector had been incorrectly installed 10 metres above ground level.
Sulphur Dioxide is a heavy gas and therefore SO2 detectors need to be mounted close to the ground level in order to provide safe protection of personnel and plant.
The solution
Due to the experience and industry knowledge of the Entec technician, this problem was identified and a solution was simply engineered. The SO2 detector is now installed in the appropriate place.
Ongoing success
The fixed gas detection system will now provide the protection that this site requires and Entec continues to provide routine service to the site.
Quick Links
In the Fixed Gas Detector Systems section of our website we have the following pages…
- Fixed Gas Detector Systems Overview »
- Fixed Gas Transmitters & Sensors »
- Fixed Gas Detection Controllers »
- Fixed Gas Detection Case Studies (YOU ARE HERE)